Milling And Flotation Of Slow Cooled Copper Slag
2020-07-28T16:07:12+00:00
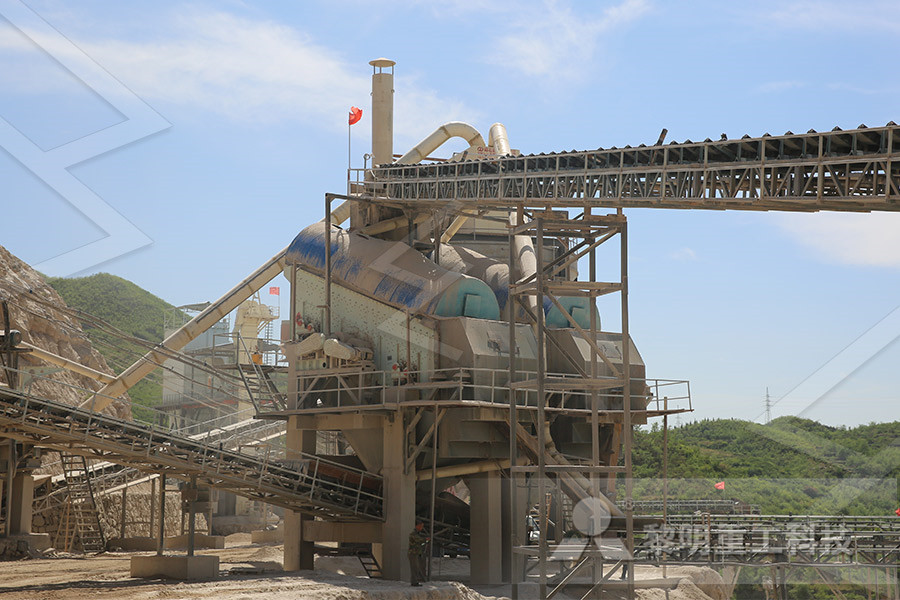
Laboratory test work and plant trials for milling and flotation
2012年9月11日 The plant trials have demonstrated that the copper recovery in the milling and flotation process of the slow cooled slags was improved by 3% Lab ball mill Copper 2012年3月17日 Laboratory Test Works and Plant Trials for Milling and Flotation of Slow Cooled Copper Slag Pengfii Tan for more papers by this author Alberto Oalvez Laboratory Test Works and Plant Trials for Milling and Flotation 2022年6月1日 In this study, a facile process for recovering copper from copper slags through flotation enhanced by sodium carbonate synergistic mechanical activation has Copper recovery from copper slags through flotation
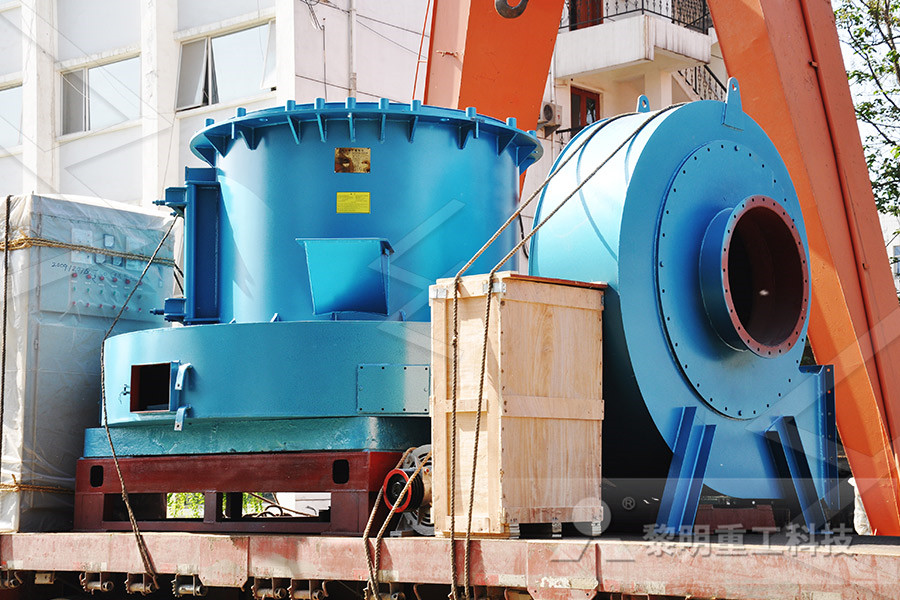
Effect of Cooling Rate and Slag Modification on the
[9, 10], and bioleaching [11] have been proposed Milling and froth flotation methods are quite common when dealing with slowcooled slags Before flotation, the slag needs to 2021年5月1日 A slow cooling rate of the molten copper slag can minimise the effect of viscosity on the mass transfer of diffusion and grain growth of matte copper (or metallic Comprehensive review on metallurgical recycling and cleaning of copper slag2020年1月1日 Therefore, the scope of the present work involves an investigation into how the flotation recoveries of the copper minerals can be enhanced by studying the Enhancing the flotation recovery of copper minerals in
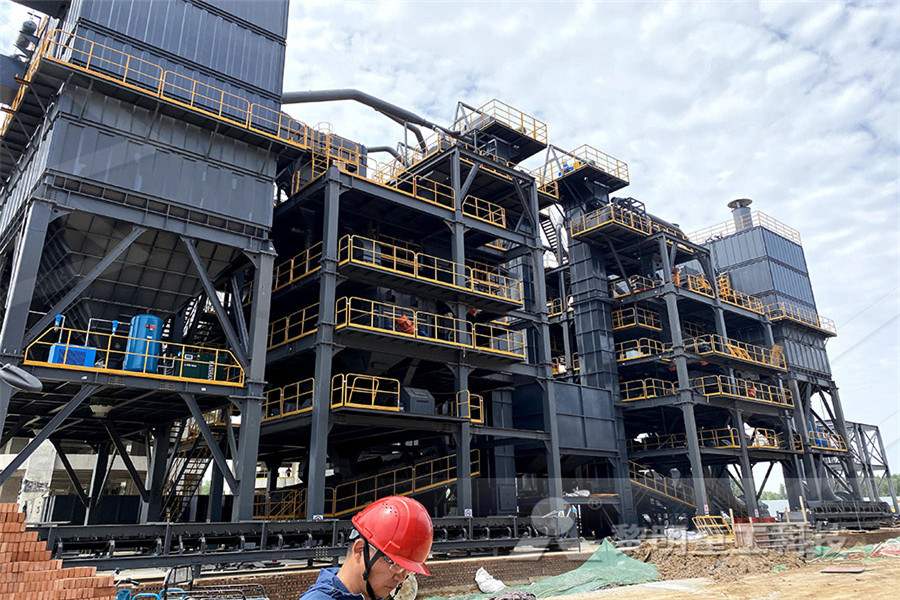
Copper recovery by flotation Springer
2017年8月29日 For instance, laboratory milling tests on converter slag produced at the Noranda smelter (15% Cu) have shown that a slowlycooled slag yielded a 04% copper 2020年11月11日 During flotation treatment of CS cooled in ponds in the Central Ural Copper Smelting Plant (SUMZ) refinement is performed to a size of –74 μm of 90–92% Processing Converter Slags with Total Utilization of AllFrom the industrial copper slag flotation campaigns, it was concluded that it is possible to obtain a commercialquality copper concentrate, suitable for further processing in a copper smelter This mitigates certain Copper Recovery Through Smelter Slag Flotation

Effect of Cooling Rate and Slag Modification on the
[9, 10], and bioleaching [11] have been proposed Milling and froth flotation methods are quite common when dealing with slowcooled slags Before flotation, the slag needs to be cooled inacontrolledmanner Therearemultipleoptionsforthis,such as natural cooling, casting mill cooling, water quenching, andAnother aspect that can affect both the milling and flotation of CS is the cooling behavior of the slag Recovery of copper from slow cooled ausmelt furnace slag by floatation Characterization of Minerals, Metals, Copper Recovery Through Smelter Slag Flotation 2019年3月15日 Tailings from an industrial copper slag cleaning milling and flotation circuit have been prereduced at low temperatures, well below its melting point, using CH 4H 2Ar mixtures with the aim of metallizing its iron oxide component to metallic ironThe treatment carried out at 700–900 °C, with a duration of up to 90 min, indicated a complete Upgrading copper slag cleaning tailings for reuse
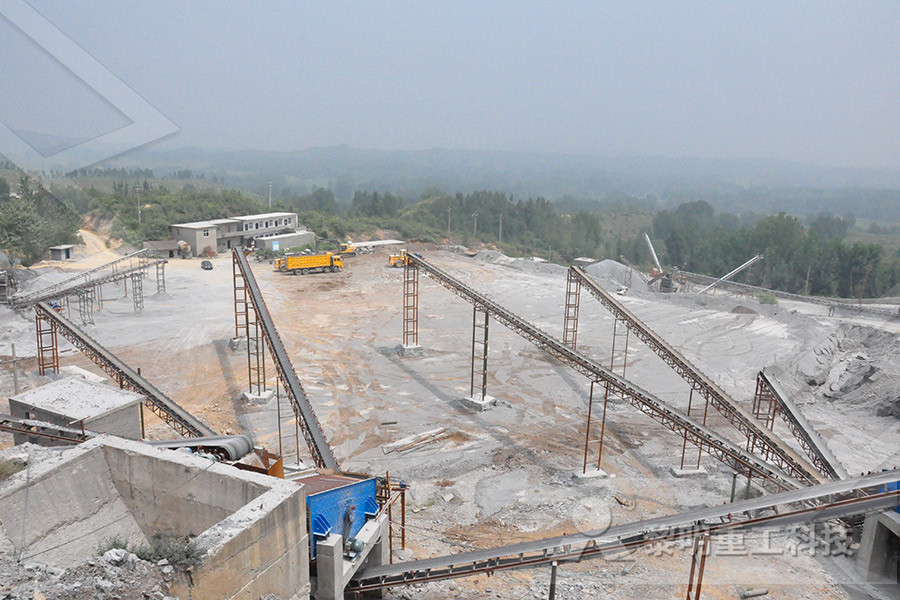
Copper Recovery Through Smelter Slag Flotation in
2022年4月8日 copper grade of 16,11% and copper recovery of 69,90% was achieved The copper grade on tailings was only 0,2% Another aspect that can affect both the milling and flotation of CS is the cooling behavior of the slag Several researchers have reported that slow cooling of the slag can lead to an improvement in copper recovery because of the 2021年10月1日 Copper slag flotation is similar to sulphide ore flotation (Osborn et al, 1990, Arslan and Arslan, 2002, Gulay, 2006) The copper slag is fed into the flotation unit and the sulphide minerals (Cu 2 S, Cu 5 FeS 4) are floated with the help of collector and frother reagents to produce a concentrateThe potential for copper slag waste as a resource for a 2017年12月1日 They used mercaptobenzothiazole (MBT) collector to recover the copper from the ground copper slag and indicated that a slowcooled slag would be more favorable for better copper recovery Flotation of ground copper slag was also studied by Bruckard et al (2004) According to them, using a twostage flotation process, 80–87% Cu can be Recovery of metal values from copper slag and reuse of
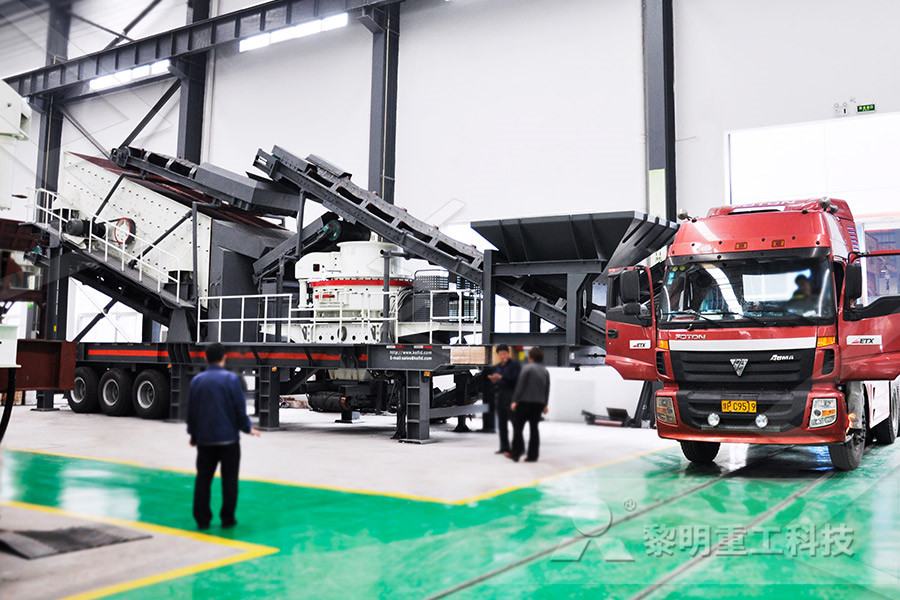
Copper Recovery Through Smelter Slag Flotation in
copper grade of 16,11% and copper recovery of 69,90% was achieved The copper grade on tailings was only 0,2% Another aspect that can affect both the milling and flotation of CS is the cooling behavior of the slag Several researchers have reported that slow cooling of the slag can lead to an improvement in copper recovery because of the Laboratory flotation tests of slow cooled converter slag have showed that 925% copper recovery at the copper cutoff grade of 24 25 % can be achieved by using a 50:50 ratio of DSP330 andLaboratory Test Works and Plant Trials for Milling and 2012年9月21日 Smelters using slag milling and flotation for slag cleaning generally operate under conditions where most of the copper in slag would tend to form Cu 2 S upon cooling, although some metallic copper may still form via reaction 37 Ideally, the slag should be slow cooled to allow most of the copper to form larger matte prills (over 30 μm in size Minimization of Copper Losses in Copper Smelting Slag
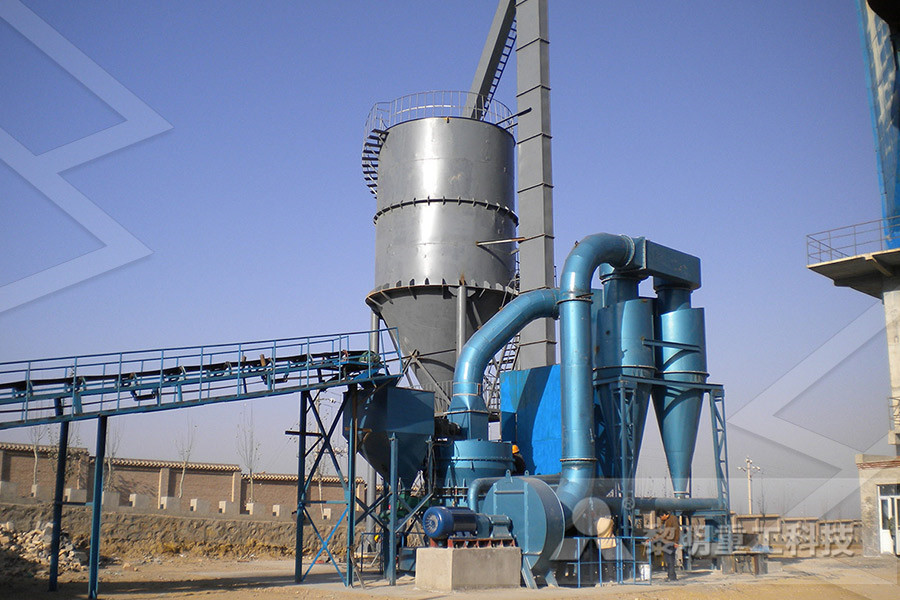
Process for controlled slow cooling of nonferrous smelting
A process for controlled slow cooling of nonferrous smelting slags, such as copper slags, for the recovery of the nonferrous metals contained therein by subsequent crushing, milling and flotation operations is disclosed The process comprises the steps of pouring the molten slag into a ladle, allowing the slag to slowly cool and solidify in the ladle at least to the point 2021年1月13日 Copper slag flotation was studied on an industrial scale at a concentrator plant in the region of Atacama, Chile Another aspect that can affect both the milling and flotation of CS is the cooling behavior of the slag Xue, P, Li, G, and Qin, Q (2016) Recovery of copper from slow cooled ausmelt furnace slag by floatation Copper Recovery Through Smelter Slag Flotation in 2012年3月17日 Laboratory Test Works and Plant Trials for Milling and Flotation of Slow Cooled Copper Slag Pengfii Tan for more papers by this author Alberto Oalvez for more papers by this author Lucya Yunus for more papers by this author Xstrata CopperLaboratory Test Works and Plant Trials for Milling and Flotation
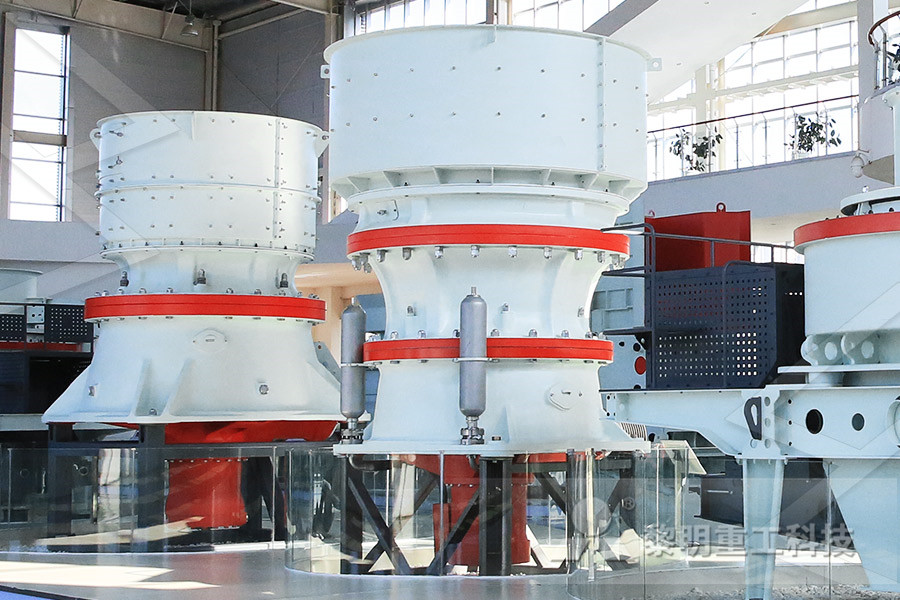
Comprehensive review on metallurgical recycling and cleaning of copper slag
2021年5月1日 Generally, slow cooling slags are more beneficial for better recovery of copper by flotation A slow cooling rate of the molten copper slag can minimise the effect of viscosity on the mass transfer of diffusion and grain growth of matte copper (or metallic copper), and further help in the subsequent fine grinding and flotation stages of copper The projected capacity of the copper slag processing is 340000 tons per year with an average copper content of about 2 % This amount of copper slag will be obtained from 290360 tons/ year from the Flash process technology with copper content of 1,4 % and 49640 tons/year from PS converter with copper content of 6 % (Sokolovic et al, 2015)SUSTAINABILITY OF COPPER SLAG PROCESSING FROM NEW 2021年12月1日 The produced slag, with iron to silica (SiO 2) plus lime (CaO) ratio of 135 went for slow cooling and slag flotation SO 2 rich offgas of the furnace was cooled in a heat recovery boiler (HRB) and further cleaned from dust in an electrostatic precipitator (ESP) before leading to an ID fan with oxygen content of 05% in the offparison of environmental performance of modern copper
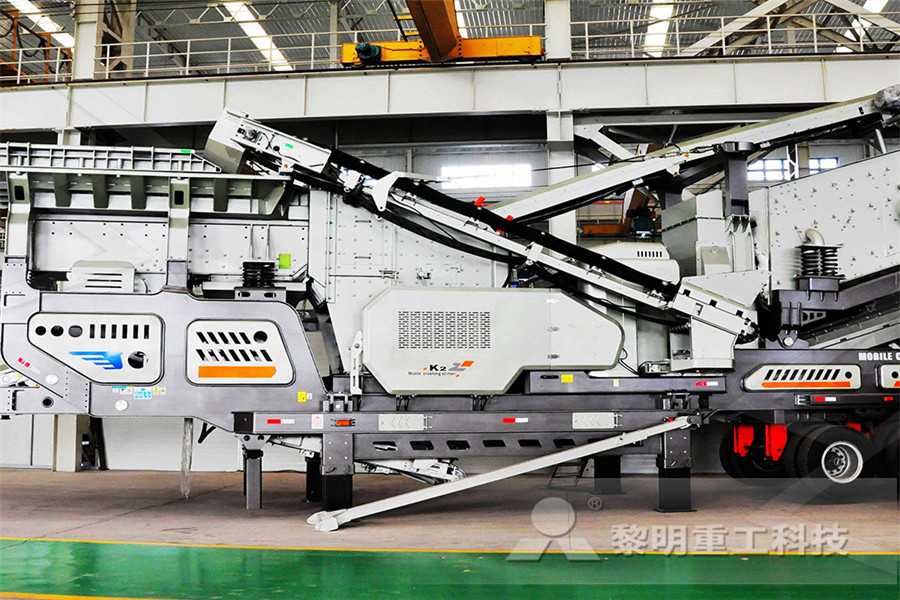
A study of the effect of grinding environment on the flotation
2018年6月15日 The nature of copper slag flotation is unique due to the high temperature in the flotation pulp and high metallic copper content in the feed Despite its great potential for valorizing slag, copper slag flotation remains challenging due to the deactivation of traditional dithiocarbonate (DTC) collectors (eg, butyl xanthate) under high temperaturesCopper slag flotation was studied on an industrial scale at a concentrator plant in the region of Atacama, Chile casting mill cooling, water quenching, and slow cooling in a ladle [12 Differences in the microstructure as a function of the cooling 2020年1月1日 Copper smelting slag is the largest solid waste produced in coppermaking process, and slow cooling beneficiation technology is the most widely used method in recovering remaining treasures from (PDF) Enhancing the flotation recovery of copper minerals in
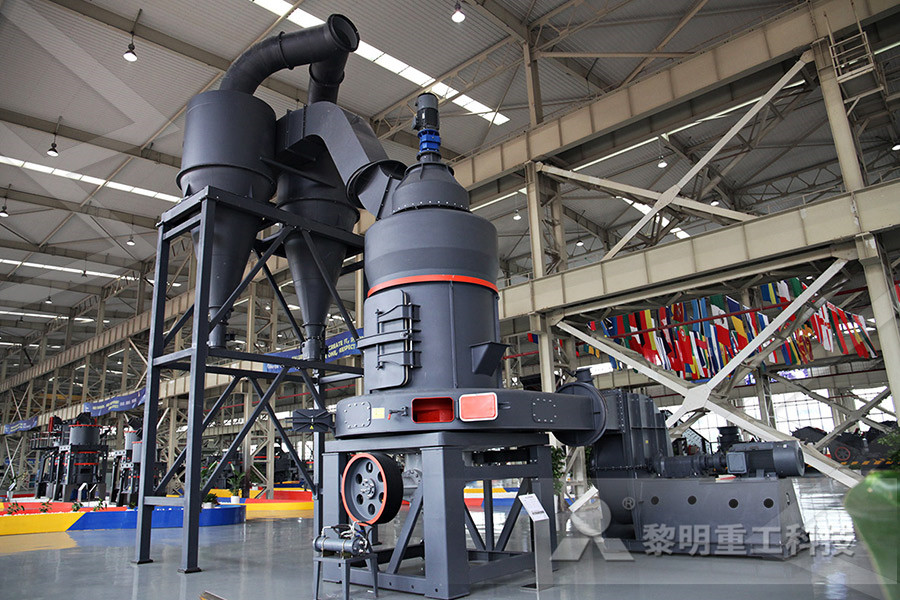
Effects of fluxing conditions on copper smelting slag
2016年12月5日 °C) with 2–3 wt% Cu remaining in the smelting slag At present, the recovery of copper from slag is processed by slow cooling, milling and flotation at Fangyuan Bottom blown oxygen copper smelting technology has demonstrated great potential and will be transferred to other plants around the World In addition to the flotation process