Grinding Wheel In Raw Mill Cement Plant
2022-10-22T16:10:45+00:00
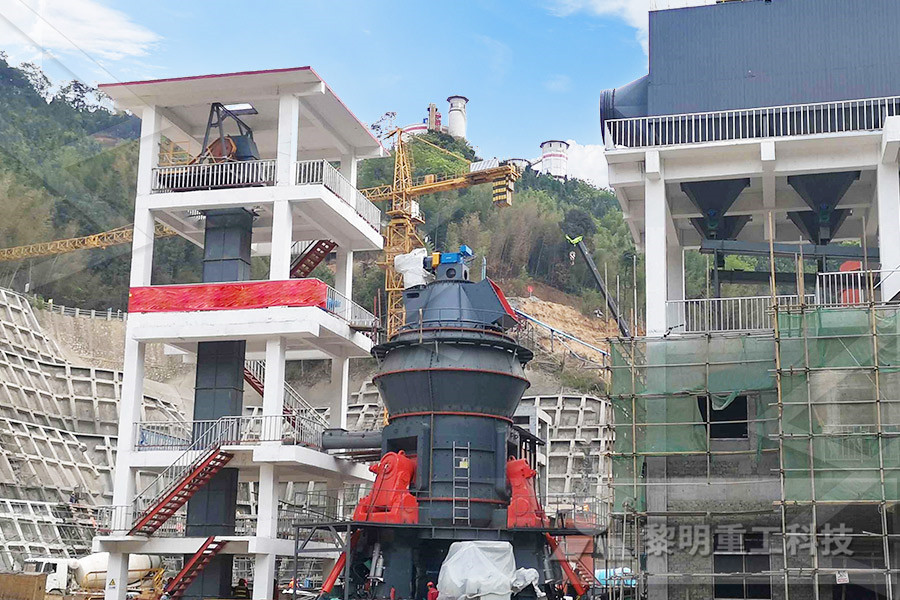
Modeling of energy consumption factors for an industrial cement
2022年5月9日 Lin, X Liang, J Modeling based on the extreme learning machine for raw cement mill grinding process in Proceedings of the 2015 Chinese Intelligent Automation 2018年7月1日 Benzer [13] studied on optimizing the fully airswept raw mill grinding circuit, Dundar et al [14] reported the optimization opportunities of a cement grinding circuit Energy and cement quality optimization of a cement grinding circuit 2022年12月19日 A raw mill is a key piece of equipment used in a cement plant to grind raw materials into a fine powder It works by crushing and grinding materials such as How does a raw mill work in a cement plant? LinkedIn
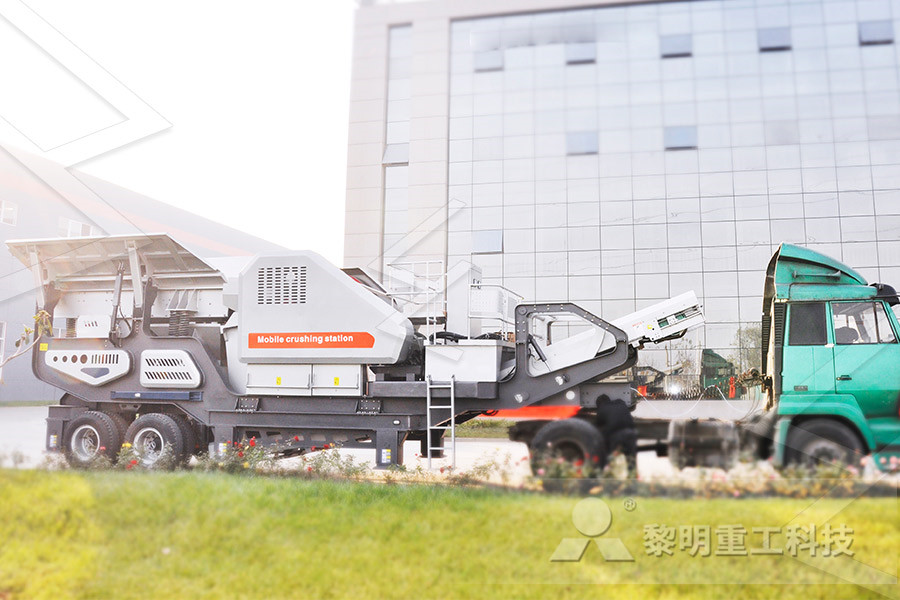
Grinding process optimization IEEE Xplore
2017年6月19日 The modular vertical roller mill for grinding cement raw material, cement clinker, and additives with an installed power of up to 12,000 kW was specifically 2016年1月20日 For the current study, eight primary units are defined: crushing materials into a crusher, grinding the raw materials in a raw mill, preheating and calcining the raw Analysis of material flow and consumption in cement2021年1月1日 Raw Meal Grinding Homogenization: Grinding Mill Vertical Roller Mill or Ball Mill: The reclaimed raw mix fed to Raw Mills, for drying and fine grinding of Raw Review on vertical roller mill in cement industry its
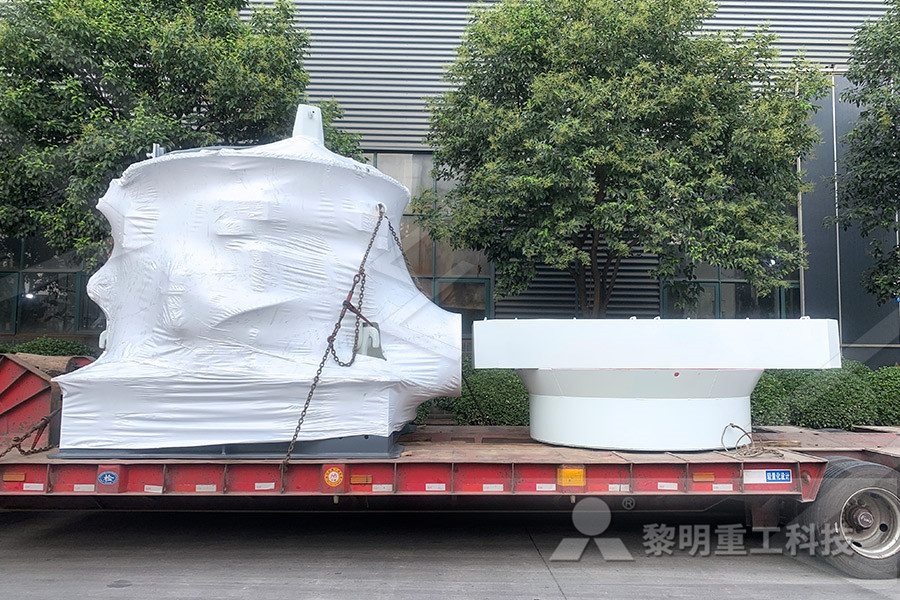
Raw Mill – Raw Mill In Cement Plant AGICO Cement Raw Mill
Raw Mill Selection Guide Raw meal grinding is a vital link in the cement raw material preparation process After the cement raw material is crushed, it will be sent into the raw 2012年6月1日 Raw mills are used to grind the raw materials into the farine which is the semi product of clinker It is then fed to the rotary burners which transforms it into clinker Reducing energy consumption of a raw mill in cement industry碾磨加工 WEG运用在磨机传动装置上的经验为矿山开采黑色及其他有色金属提供了最为可靠和高效的解决方案。 对一个加工厂来说,加工过程中球磨机和半自磨机的使用方案必须 矿业 碾磨加工 WEG
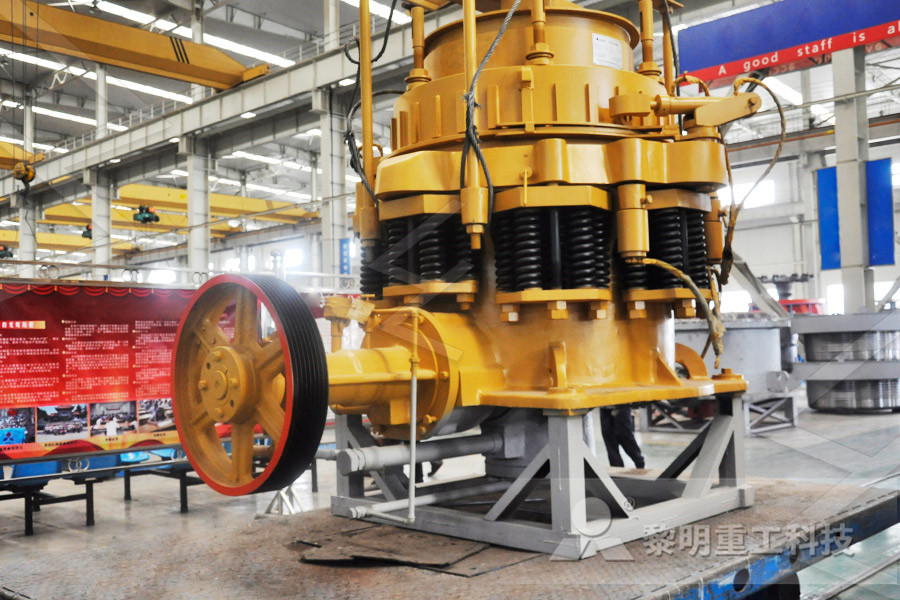
The Hydraulic Roller Press offers costsaving grinding
The Hydraulic Roller Press has the capability to grind raw material, cement clinker or slag and is suitable even for dry feed materials and there is no need to add water to the roller press while processing Improve production while reducing energy consumption The flexible Hydraulic Roller Press is suitable for both upgrades and new installationsBall mills for cement raw material and coal equipped with a drying compartment adequately air swept with hot gas (2535M/sec above the ball charge), can handle moisture about 8% Fully air swept mills (56M/sec) can dry up to 1214% moisture Grinding Operation Objectives and KPIs: Highly energy intensive unit operation of size reduction in Raw Material DryingGrinding Cement Plant OptimizationThe vertical roller mill (VRM) is a type of grinding machine for raw material processing and cement grinding in the cement manufacturing processIn recent years, the VRM cement mill has been equipped in more and more Vertical Roller Mill Operation in Cement Plant
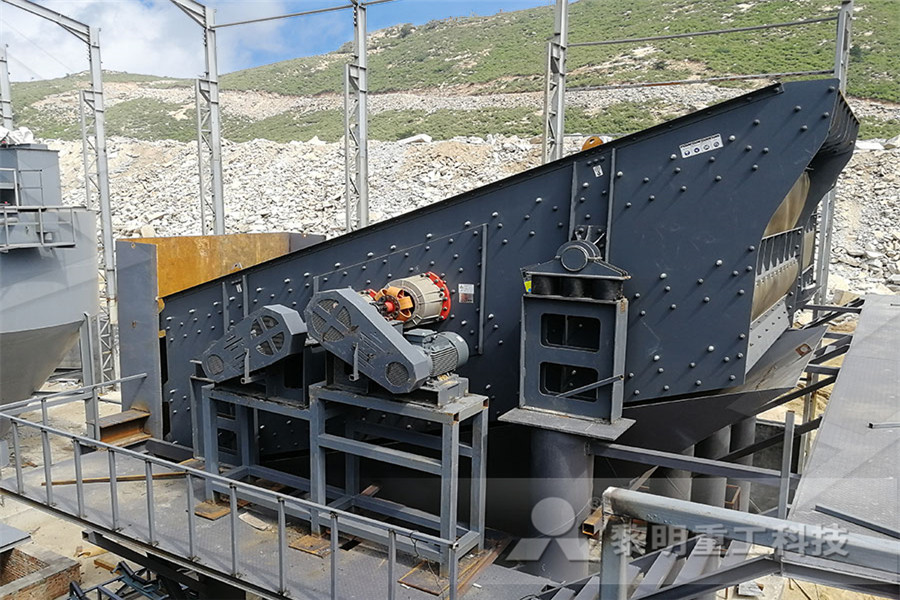
Reducing energy consumption of a raw mill in cement industry
2012年6月1日 Several grinding methods are available in cement industry depending upon the material to be ground In cement production process, about 26% of the total electrical power is used in grinding the raw materials During grinding process, the energy obtained from the rotary burner is consumed In this study, the first and second law analysis of a 2018年7月1日 Energy optimization of a circuit has been subject of many of the studies Jankovic et al [12] considered the optimization alternatives of cement grinding circuits Benzer [13] studied on optimizing the fully airswept raw mill grinding circuit, Dundar et al [14] reported the optimization opportunities of a cement grinding circuitEnergy and cement quality optimization of a cement grinding circuit 2015年2月16日 The most obvious area for attention is that of grinding, both raw and cement In either case, grinding is, by design, a very inefficient process Figure 2: breakdown of electrical energy consumption at a typical cement plant Plant 3 – Vertical mill (kWh/t cement) CPJ 35 308 298 304 CPJ 45 325Best energy consumption International Cement Review

EnergyEfficient Technologies in Cement Grinding IntechOpen
2016年10月5日 The energy consumption of the total grinding plant can be reduced by 20–30 % for cement clinker and 30–40 % for other raw materials The overall grinding circuit efficiency and stability are improved The maintenance cost of the ball mill is reduced as the lifetime of grinding media and partition grates is extended 25Raw meal grinding is a vital link in the cement raw material preparation process After the cement raw material is crushed, it will be sent into the raw mill for further grinding until a certain degree of fineness is reached, and then enter the clinker calcination process From the production experience of many cement plants, the selection of Raw Mill – Raw Mill In Cement Plant AGICO Cement Raw Mill2023年10月3日 Cement Industry LOESCHE Vertical Roller Mill: We do much more than rely solely on our unbeatable technology Our designers are constantly coming up with new ideas and even more dependable components to reduce the already acclaimed low failure rate of our mills The roller grinding mill technology, patented in 1928 and continuously Cement Industry Loesche
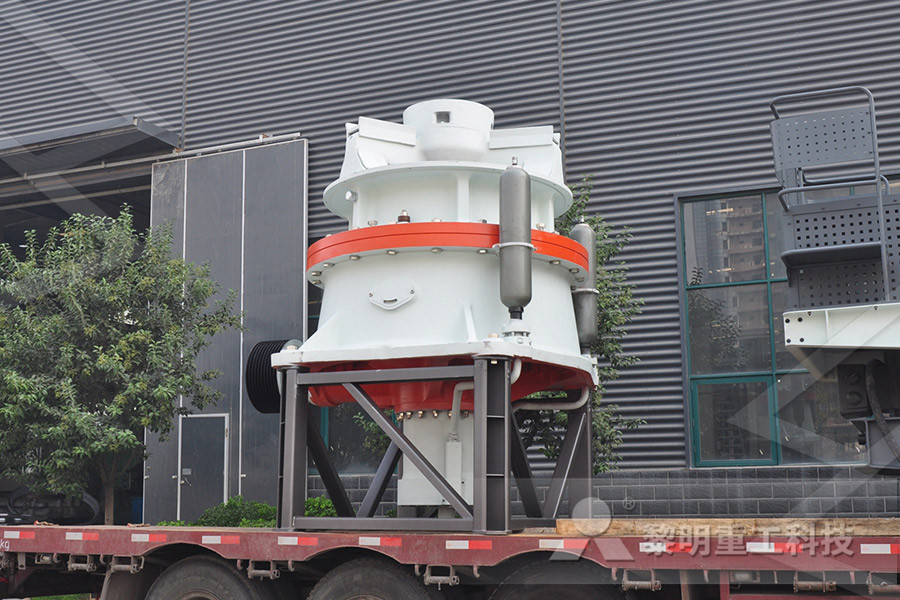
Analysis of material flow and consumption in cement
2016年1月20日 In the surveyed cement plant, three balances are established between input and output material in the raw mill, clinker production, and cement grinding system 248 t, 469 t, and 341 t of materials are required to produce a ton of the product in raw material preparation, clinker production, and cement grinding stages; waste gases 2020年2月9日 The proportioned raw materials are then transported by a conveyor belt to the raw mill to be ground into the powder form After grinding, the powdered raw mix is stored in a raw mealsilo where A Review on Pyroprocessing Techniques for The cement raw mill is the primary piece of equipment used in the modern cement industry for the raw meal production process As a result, it is critical to investigate the exergy efficiency in a cement raw mill in order to satisfy the need for the design and optimization of the cement plant manufacturing processFull article: Evaluation of optimization techniques for
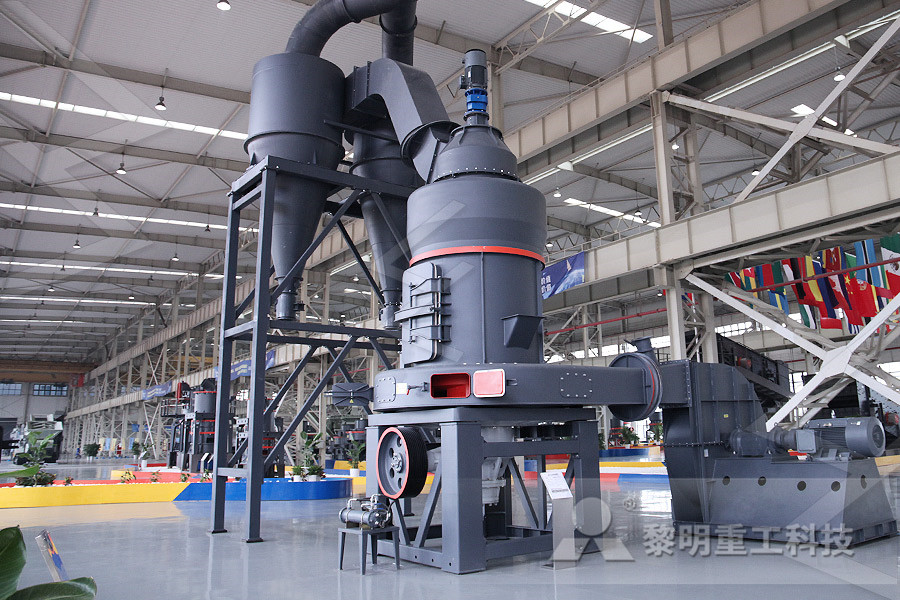
Modeling of energy consumption factors for an
2022年9月12日 80 mm e raw materials were mixed in a certain proportion and fed into a vertical roller mill (LOESCHE mill) e raw vertical roller mill has four rollers, 3000 KW main drive, 48 m table diameter 2023年3月1日 β [1 − α; p 2; n − p − 1 2] = (1–α) th quantile of β [p 2; n − p − 1 2] distribution For α = 005, the number of outliers is 44 among 280 data corresponding to an upper limit control U C L M a h a l a n o b i s = 455 as illustrated in Fig 3The results of these outliers have been carefully analyzed by a process expert from the cement plant Efficient machine learning model to predict fineness, in a vertical raw Coal mill is the main equipment in the pulverized coal preparation processBecause calcining topgrade cement clinker requires a stable supply of coal powder as the fuel of cement kiln, and more than 85% of pulverized coal should be finer than 200 mesh, water content less than 2%, and calorific value more than 6000Kcal/kg, therefore the pulverized coal Cement Mill Cement Grinding Machine Cement Plant
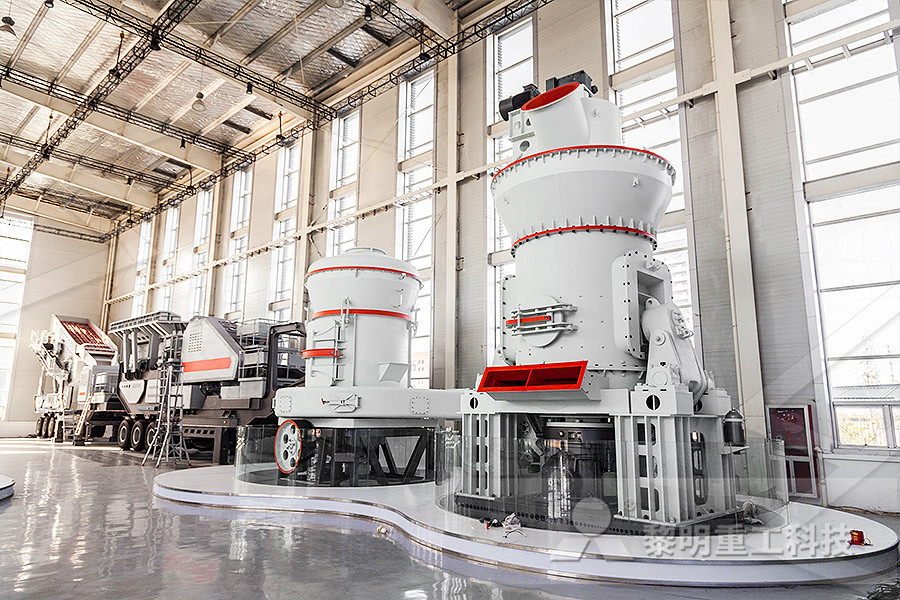
(PDF) Analysis of Raw Mill Machines Maintenance in Cement Industry
2020年5月30日 The raw mill machine functions as a main material grinder in the initial milling process such as limestone, silica stone, clay, and iron sand to become raw mix To find out the frequency of damage 2017年4月1日 Vertical roller mills (VRM) have found applications mostly in cement grinding operations where they were used in raw meal and finish grinding stages and in power plants for coal grinding The mill combines crushing, grinding, classification and if necessary drying operations in one unit and enables to decrease number of equipment in grinding Operational parameters affecting the vertical roller mill 2021年1月1日 Now a days Cement plants are producing 75–80% PPC 20–25% OPC due to high market demand of PPC Production of PPC is cheaper and it's market rate is also lower than OPC by nearly 25 rupees per bag, so general consumer are attracted towards PPC cement Cement companies also want to produce more and more PPC gradeReview on vertical roller mill in cement industry its

How to choose proper grinding media for your ball mill
2021年2月24日 There are three types of grinding media that can be used in ball mills of cement plants 1 Steel Balls Steel balls are one of the most widely used grinding media in cement ball mills, their diameters can range from 20mm to 120mm according to different grinding requirements In a cement ball mill, generally, φ50–100mm steel balls are used