Performance Evaluation Of Ball Mills
2020-09-14T12:09:58+00:00
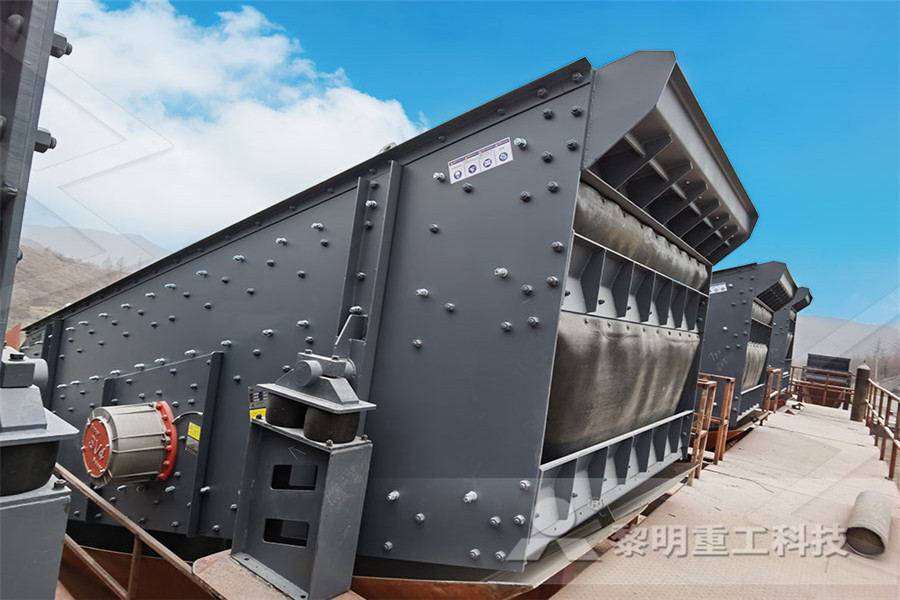
(PDF) EVALUATING THE PERFORMANCE OF A
1988年9月25日 September 1988 Authors: Etim Bassey W J Adisa Abstract An investigation of the performance of an operating commercial 2020年1月1日 A study of the laboratory ball mill performance for different mill speeds operating with and without lifters (cap open and cap close) at the discharge end has A comparative study on a newly designed ball mill and the 2017年1月1日 Performance optimization of an industrial ball mill for chromite processing Authors: Santosh Kumar Tripathy Group of (PDF) Performance optimization of an industrial
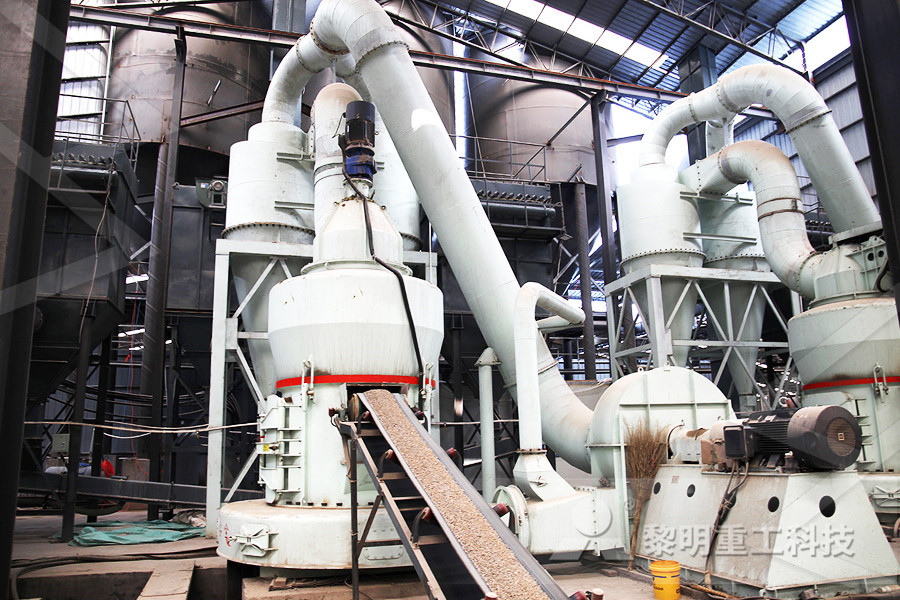
Ball mill abrasion test (BMAT): Method development and
2022年1月1日 A hypothesis was developed in the literature studying the tumbling grinding mills such as ball mills, SAG mills and rod mills to explain ‘compressed performance This article is part of the themed collection: Mechanochemistry Planetary ball mills are well known and used for particle size reduction on laboratory and pilot scales for decades Process engineering with planetary ball mills RSC Publishing2020年5月27日 geometrical lifter structure and to improve the performance of the ball mill Keywords: ball mill; DEM; heightwidth ratio; rectangular lifter; number of lifter 1 Study on the Performance of Ball Mill with Liner
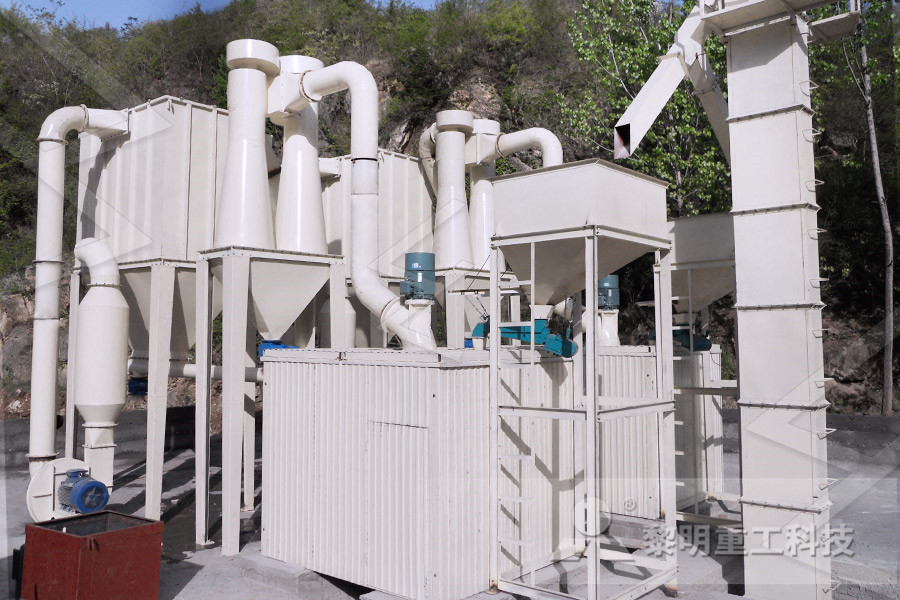
Effect of ball size and powder loading on the milling
2013年12月1日 The ball mill process is very complicated process governed by many parameters, such as ball size, ball shape, ball filling, slurry loading (with respect to ball 2015年1月1日 The effect of mill speed, grinding time, and ball size on the performance of the ball mill was investigated and the product was further investigated in the second A specific energybased size reduction model for batch grinding ball mill2021年2月19日 Optimization results confirmed that the balls to powder weight ratio were the most influential process parameter The optimum process parameters setting Comparative Study on Improving the Ball Mill Process
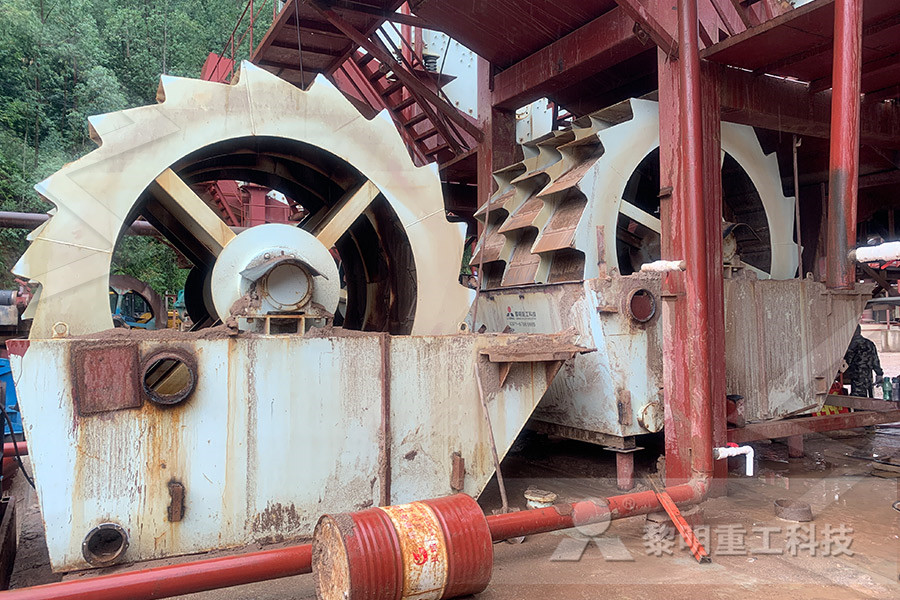
Comparative Study on Improving the Ball Mill Process
2021年2月19日 Taguchibased experimental design technique has been a major research area for making systematic approaches to understand the complex process of ball mill process parameters influencing on the synthesis of ultrafine silica sand monolayer degradation To determine an optimal setting, Taguchi coupled optimization technique 2009年6月1日 A comparative analysis of the ball mill and stirred mill performance and energy consumption at different grinding time intervals was also performed It was found that the ball mill consumed 5467 kWh/t energy to reduce the F 80 feed size of 7222 µ m to P 80 product size of 2754 µ m while stirred mill consumed 3245 kWh/t of energy to Comparison of energy efficiency between ball mills and stirred mills 1988年9月25日 Abstract An investigation of the performance of an operating commercial ball mill in a pelletising installation is reported The pattern of ball size distribution inside the mill and the effect (PDF) EVALUATING THE PERFORMANCE OF A
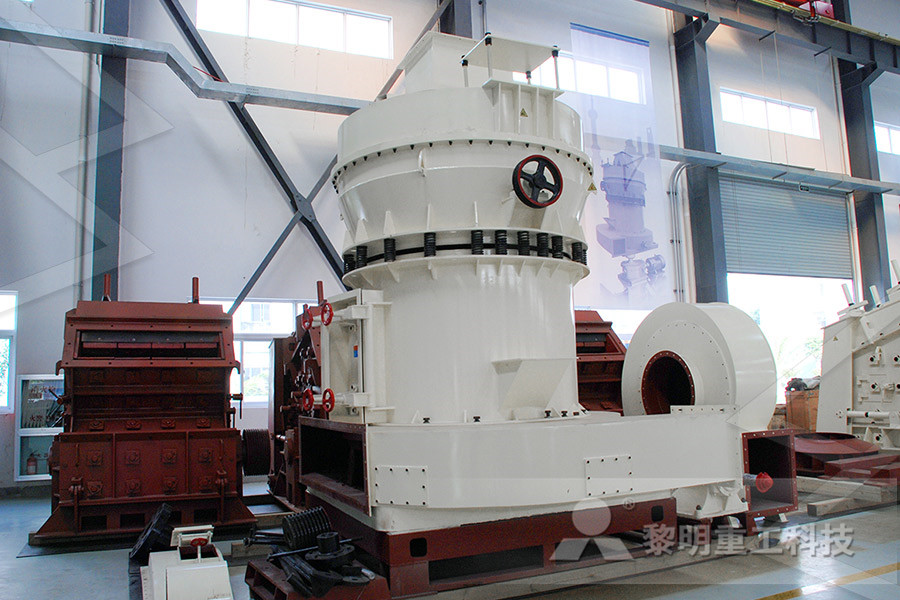
How to Improve Ball Mill Performance 911 Metallurgist
2017年10月25日 Ball Mill Breakage Efficiency Consider a ball mill circuit processing material of a given feed size and at a given throughput rate to a target product size, the latter which once again distinguishes the “fines” from the “coarse” material The production rate of fines or new product size material can be calculated from the circuit feed 2008年9月1日 Section snippets Interpretation The experiments were performed on a tubular ball mill of a 250 MW power plant unit (see Fig 1) The mill has a diameter of 32 m and a length of 47 m, and driven by a motor (YTM5006)The nominal revolutions per minute (rpm) of this mill was 1842, and the mill power draft 710 KWThe mill was Experimental investigation of vibration signal of an2018年7月22日 A ball mill is unsuitable because it has a low rotating speed, leading to lower extraction efficiency [15,17] A hammer mill is not recommended due to the health hazard of fine product pollutants (PDF) Development and Performance Evaluation of Improved Hammer Mill
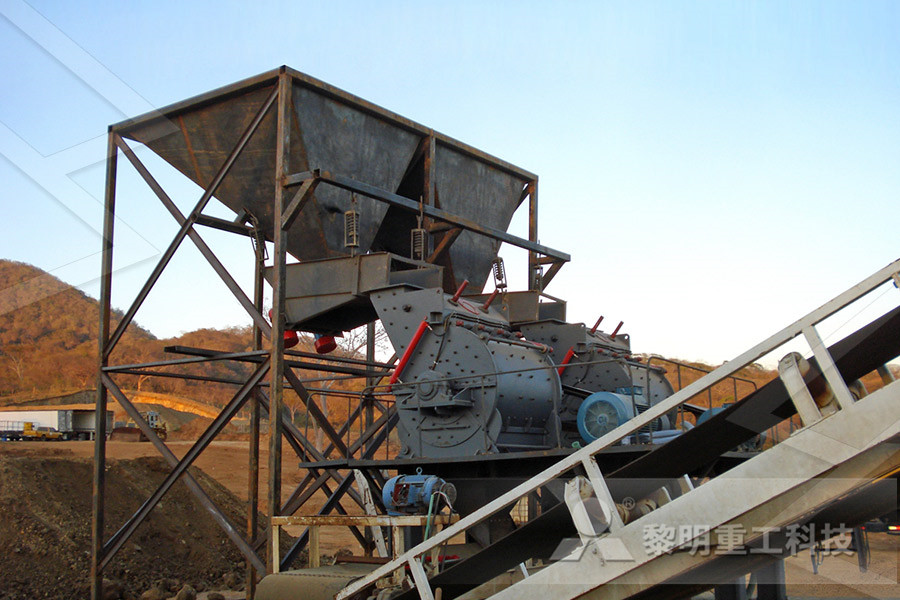
A Technical and Economic Comparison of Ball Mill Limestone
2021年10月13日 A significant power saving of 392% was observed for the dry VRM compared to the wet ball mill (377% for the circuit) The capital investment for the dry Loesche VRM circuit was found to be 105% more expensive than that of a wet milling circuit, while the reduced power consumption combined with the decrease in grinding 2015年12月27日 was selected as a criterion for the performance evaluation It was observed that in a mill with the combined makeup balls the amount of fine produced was 4% higher than the other mills The consumption of ball types A, C and D were 730, 710 and 534g/t, respectively The results of laboratory flotation tests showedTechnical Note Effect of ball size change on the 2023年1月1日 A comparative analysis of the ball mill and stirred mill performance and energy consumption at different grinding time intervals was also performed It was found that the ball mill consumed 5467 kWh/t energy to reduce the F 80 feed size of 7222 µ m to P 80 product size of 2754 µ m while stirred mill consumed 3245 kWh/t of energy to Size reduction performance evaluation of HPGR/ball mill and
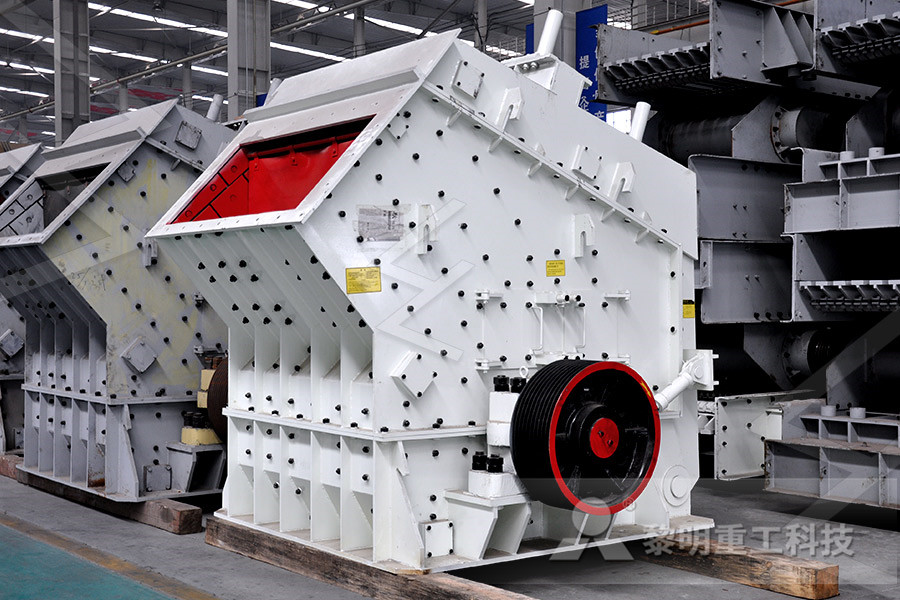
(PDF) Process Engineering with Planetary Ball Mills
2013年2月7日 While ball mills are most widely employed as a source of mechanical energy for various mechanochemical reactions [3] [4] [5][6], some other experimental apparatuses have also made remarkable 2018年9月26日 A laboratoryscale tumbling rod mill was designed for this study, and six operative parameters were tested and analyzed in order to detect the main influences on the mill product, attending to (PDF) Analysis of process of grinding efficiency in 2021年7月31日 261 Ball size distribution in tumbling mills 37 262 Milling performance of a ball size distribution 40 27 Summary 41 Chapter 3 Experimental equipment and programme 43 31 Laboratory grinding mill configuration 43 32 Preparation of monosize grinding media 44 33 Feed material preparation 46EFFECT OF BALL SIZE DISTRIBUTION ON MILLING

Ball milling in organic synthesis: solutions and challenges
During the last decade numerous protocols have been published using the method of ball milling for synthesis all over the field of organic chemistry However, compared to other methods leaving their marks on the road to sustainable synthesis (eg microwave, ultrasound, ionic liquids) chemistry in ball mills is rather underrepresented in the 2022年5月31日 To testify the reliability and availability of proposed approach in this paper, GAIFCMIDHGF is used to evaluate the current running status of coal mill by giving a mark, and the main evaluation index RMSE, FDR and FAR are adopted to demonstrate this method’s effective According to the actual condition of coal mill and professional theory A brannew performance evaluation model of coal mill 2002年4月1日 Moreover, the laboratoryscale mill uses a ball size distribution with a smaller top ball size, which also alters the breakage regime in these two mills The earliest scaleup model for prediction and design of the performance of an industrialscale ball mill was formulated by Bond, 1952, Bond, 1960, a procedure that evolved from the classical A direct approach of modeling batch grinding in ball mills
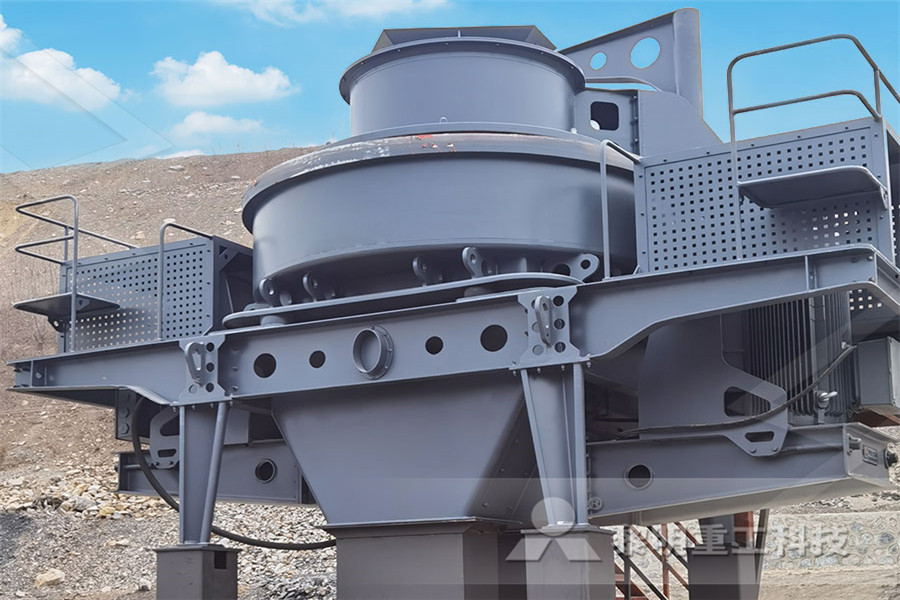
Review of control and fault diagnosis methods applied to coal mills
2015年8月1日 They are commonly known as ball and tube mills It is the oldest and the most frequently used pulverizer design As described by J Kitto and S Stultz [7], it consists of a horizontal hollow cylinder, partly filled with small diameter balls, which rotates around its longitudinal axisThe balls generally fill 25–30% of the cylinder volumeIndex I values for the Disk mill were 253625 and 243342 par/kWh at 12 mm clearance distance for Benue Yam chips and Delta Yam chips, respectively The results indicated that hammer mill performed better overall than the disk mill The comparative technique was found suitable in the evaluation of the performance of the millsA Comparative Technique for Performance Evaluation of Hammer Mill 2020年9月22日 6 Ball mill for cement grinding Ball mill This modular o™ ering performs complex and continuous evaluation of process conditions and responds with the required control and consistently than is possible for human operators This highlevel control system ensures you achieve optimum mill performance, giving you the quality, e ciency Ball mill Superior cement quality, More fl exibility, higher
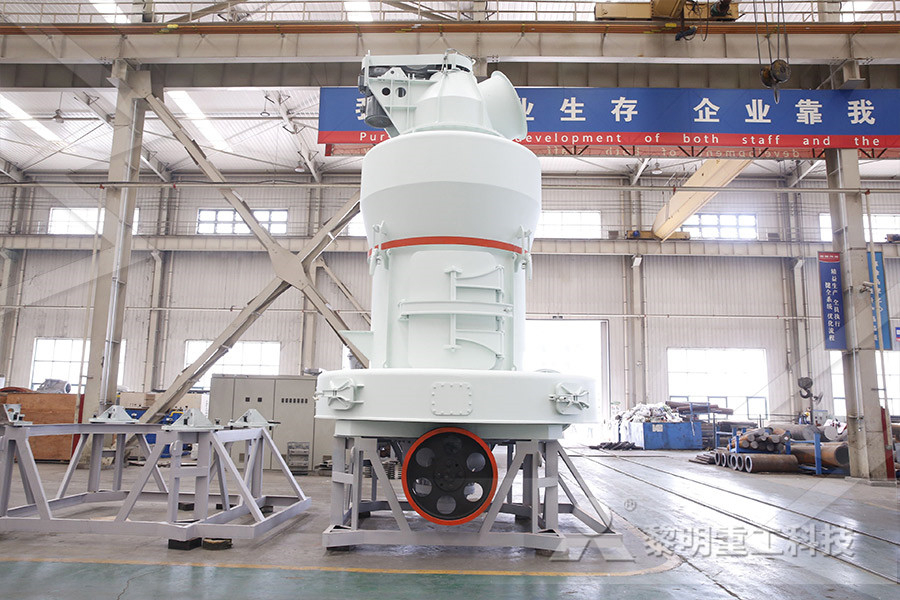
Necessity of multidimensional evaluation of the highspeed ball
2019年5月17日 This paper focuses on revealing the anisotropy of surface integrity and wear resistance of highspeed ballend milled surfaces of hardened cold work die steel AISI D2 Dry milling tests were performed on a fiveaxis highspeed machining center by using a twoedged coated solid carbide ballend milling cutter Then, wear resistance of a hard 2011年1月1日 The purpose of the study is to assess the grinding and classification performance of a conventional Polysius® twocompartment ball mill and a Sepol® dynamic air classifier closed circuit process Grinding performance evaluation of twocompartment cement grinding ball